In an age of mass production, Dutch brand Wandler stands apart with its quiet dedication to craftsmanship. In this installment of From Needle to Thread, we go behind the seams with Wandler’s Italian artisans to uncover the eight-hour journey it takes to bring the iconic Hortensia Bag to life—from premium calfskin to polished masterpiece.
A modern icon, rooted in craft
The Hortensia Bag is more than just an accessory—it’s a manifesto. As the debut design from Amsterdam-based label Wandler, the bag has become a staple in the wardrobes of discerning fashion lovers. But beyond its sleek silhouette and architectural flair lies a meticulous process that takes nearly a full working day to complete.
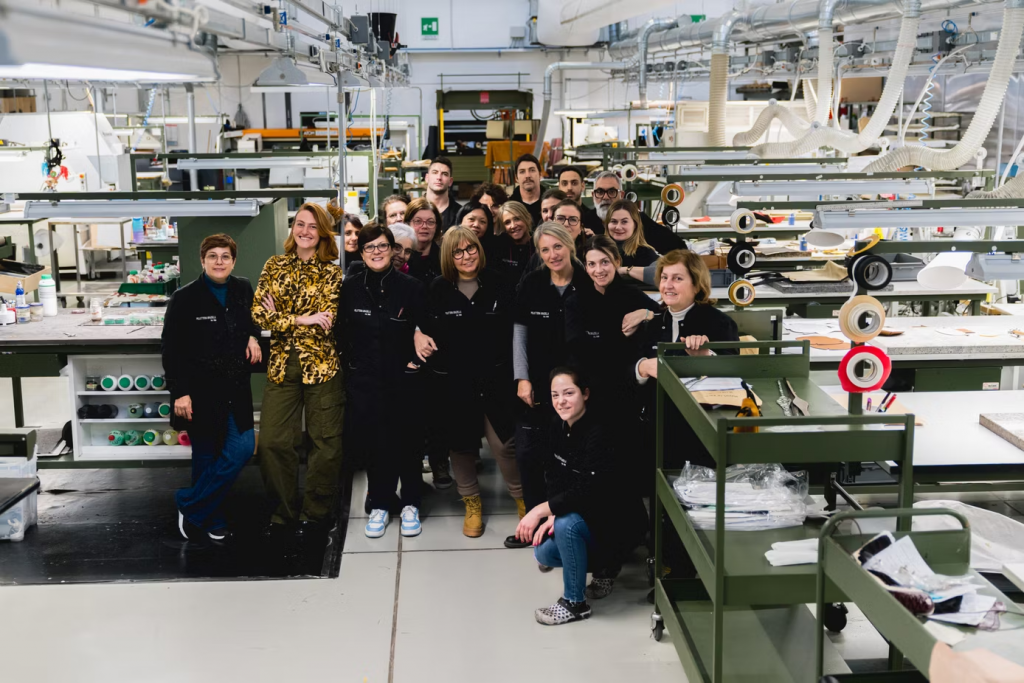
Every Hortensia Bag is handcrafted in Italy, where a select team of artisans oversees its production from start to finish. The effort is part of Wandler’s unwavering commitment to quality, sustainability, and timeless design. “We never wanted to chase trends,” said founder Elza Wandler in previous interviews. “We wanted to create pieces that people would treasure for years.” That ethos is reflected in the bag’s construction—a blend of heritage techniques and contemporary minimalism that feels both luxurious and utilitarian.
It begins with the leather
“Every masterpiece begins with the quality of the material,” says a lead artisan from Wandler’s Italian production team. And indeed, the process of making a Hortensia Bag begins long before any stitching takes place.
The bag uses exclusively Italian calfskin leather (Vitello), sourced from suppliers certified by the Leather Working Group (LWG)—a global organization promoting sustainable environmental practices in leather production. These hides are a byproduct of the food industry, sourced from cattle bred under strict European Union standards. For Wandler, ethical sourcing is as much a priority as aesthetics.
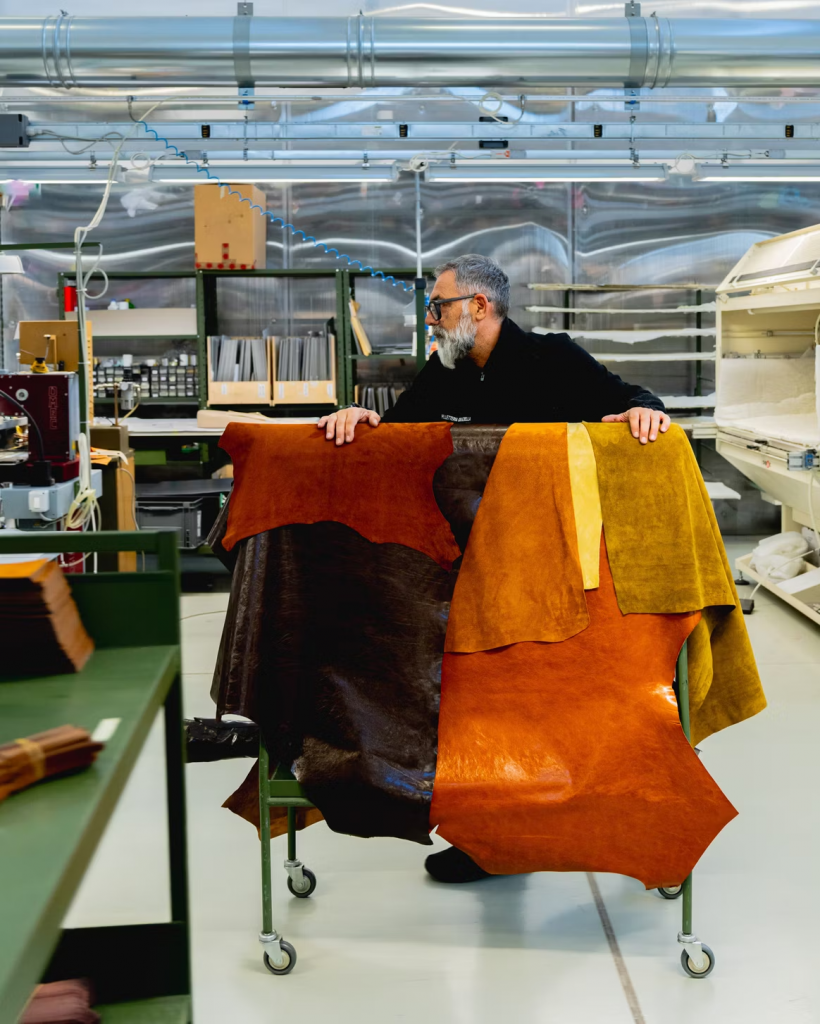
Once selected, the leather is custom-dyed for Wandler. The label is known for its vibrant yet refined palette—think moss green, dusty rose, terracotta, and bone white. These colors aren’t chosen randomly; each hue goes through a rigorous approval process to meet Wandler’s high standards and to complement the brand’s seasonal and signature offerings.
Shaping the signature silhouette
After the leather is dyed and dried, it’s time to cut it. This stage requires a mix of precision and artistry. The leather is carefully sliced into individual components, including the rounded main body of the bag and the iconic “wings” that fan out from its sides—a defining feature of the Hortensia silhouette.
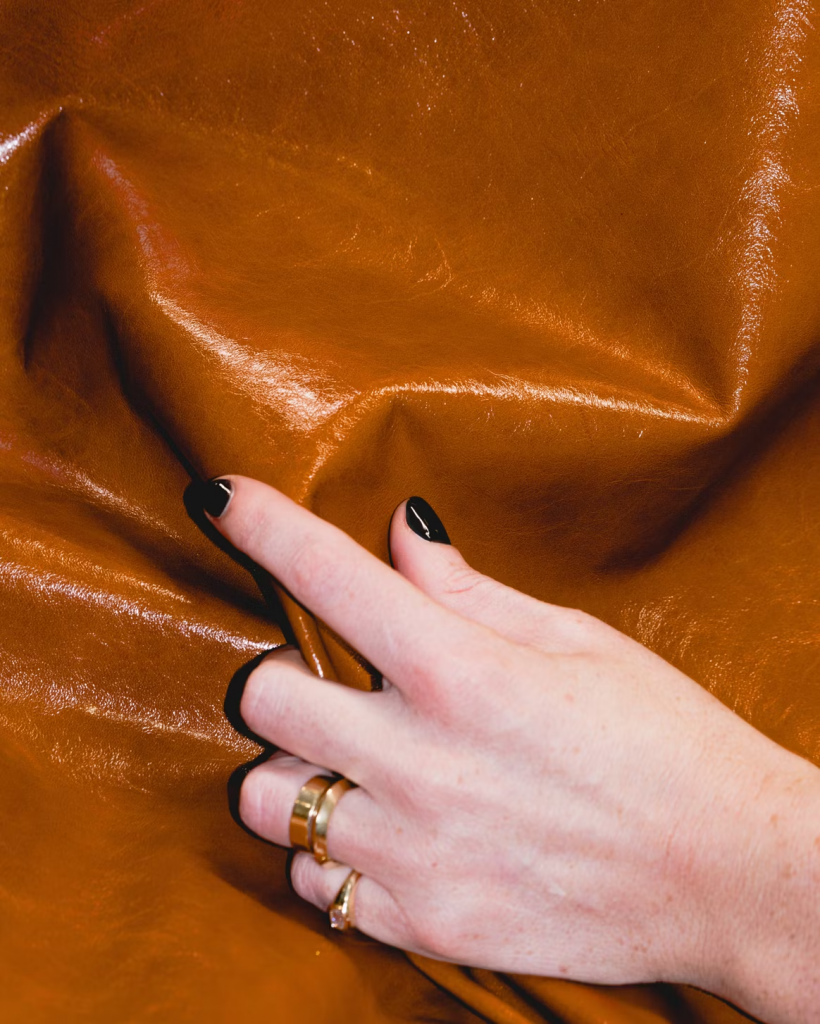
Unlike mass-manufactured accessories that rely on automated cutters, each Hortensia piece is cut with attention to the grain, stretch, and character of the leather. “It’s not just about cutting shapes,” explains one artisan. “It’s about finding the right part of the hide for each component. That’s what gives the bag its smooth structure and longevity.”
Once cut, the pieces are examined and hand-prepared for assembly, which begins with heat-stamped branding. The Wandler logo and a discreet “Made in Italy” tag are pressed into the leather using gold foil—an old-world technique that adds subtle shine and authenticity.
Hardware and handwork
Next comes the hardware. Gold-tone accents such as magnetic closures, clasps, and zippers are attached, aligning with the bag’s refined yet functional ethos. These components are sourced from Italian metalworkers and chosen for both aesthetic and durability. They’re not just decoration—they’re integral to the user experience of the bag.
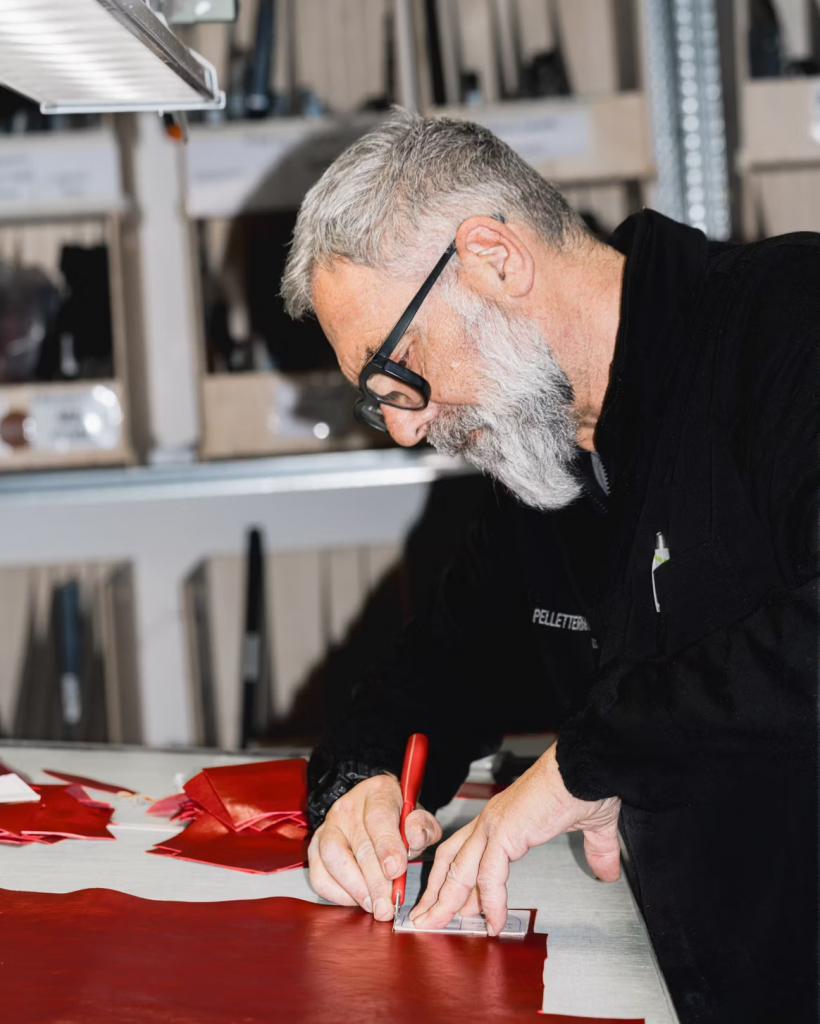
From there, the bag begins to take shape. The individual pieces—body, wings, flap, pockets—are hand-stitched or glued together in sequence. Each seam is reinforced to ensure structural integrity. Perhaps the most delicate stage is the finishing of the edges: every edge is hand-painted with black lacquer, layer by layer, giving the bag a crisp, high-gloss finish that won’t chip over time.
This attention to detail is what gives the Hortensia its unmistakable sense of polish. It’s also what makes each bag slightly unique—no two are exactly the same, thanks to the hand-crafted process.
Function meets form
Though the Hortensia Bag makes a strong visual statement, it’s also designed to be practical. Available in two sizes—mini (€795) and medium (€895)—the bag includes multiple compartments for easy organization. It comes with both a short top handle and an adjustable shoulder strap, offering versatility in styling and use.
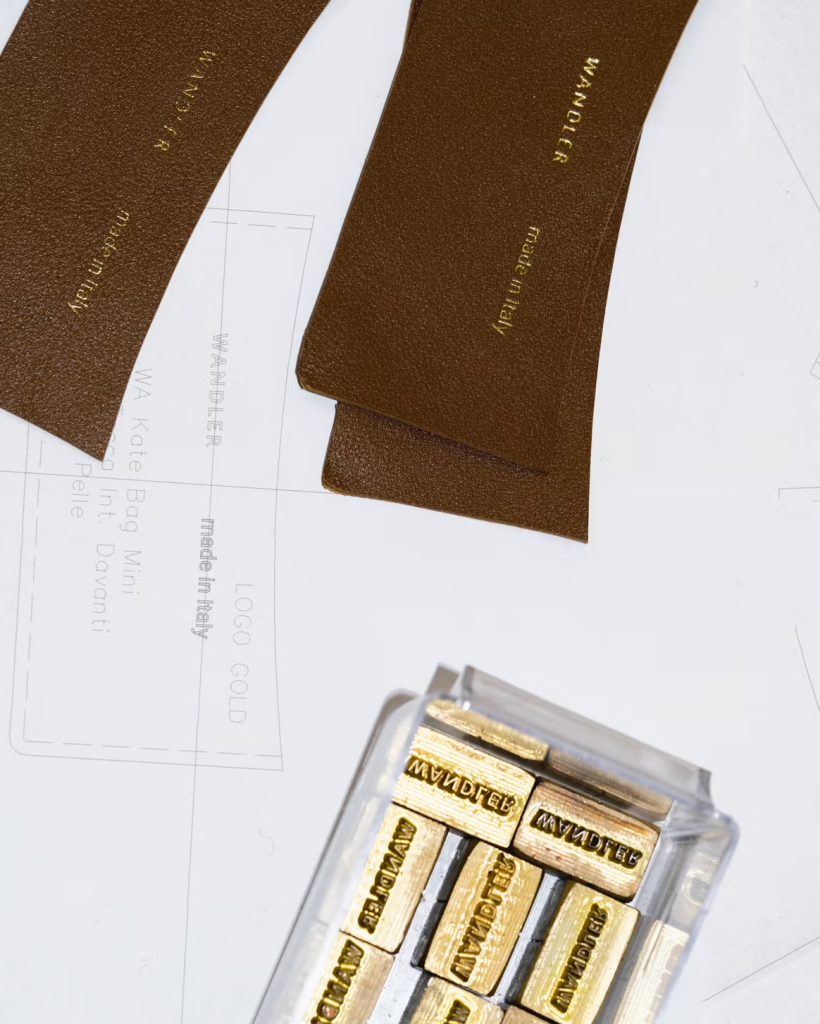
The medium size comfortably holds everyday essentials like a phone, wallet, keys, and sunglasses. The mini, while more compact, is still spacious enough for on-the-go minimalists. Both styles are finished with a soft suede lining and a secure flap closure. “Our customers aren’t just buying a beautiful object,” says a Wandler team member. “They’re buying a product they can actually use every day, without compromising on elegance.”
A commitment to conscious luxury
In a fashion landscape increasingly dominated by speed and scale, Wandler’s Hortensia Bag offers a different kind of story—one that speaks to the enduring value of craftsmanship and transparency. The fact that it takes up to eight hours to produce a single bag is not a limitation—it’s a testament.
By keeping production small and intentional, Wandler avoids overstock and excess waste. The brand also champions long-term use: instead of chasing fleeting trends, its designs are made to be relevant for years to come.

The success of the Hortensia Bag—and Wandler’s broader appeal—suggests a growing appetite among consumers for this kind of slow fashion. It’s not just about the product, but the process. And in Wandler’s case, that process is as thoughtful and beautifully constructed as the bag itself.
At a time when fashion is speeding up, Wandler invites us to slow down—to savor each stitch, each curve, and each thoughtful choice. The Hortensia Bag may be a quiet luxury, but its craftsmanship speaks volumes.